A typical warehouse includes dozens of individual processes, each of which is associated with a cost. Planning for warehouse improvement involves exploring the fine details and quantifying each process, then linking it with a KPI. Monitoring the following KPIs gives you accurate insight into your strengths, weaknesses and opportunities for change, allowing you to implement an effective improvement strategy.
1) Time Taken To Receive Goods
A lot of improvement plans focus on what happens within the warehouse, e.g. picking, packing and shipping. However, the time taken to receive goods is also important. This starts with how much time your suppliers’ delivery vehicles spend at the warehouse docks. Simply measuring this figure can give you several important insights about your warehouse, for instance:
- Is your goods receiving team adequately staffed?
- How productive are your team?
- Do you have sufficient infrastructure to receive goods?
- How well utilised are your docks and goods receiving areas?
- Are your facilities (i.e. dock or door types) suitable for your suppliers’ vehicles?
- Are your suppliers' delivery windows well suited to your staffing pattern?
2) Time To Pick, Pack & Ship Orders
A key metric involves how much time it takes to retrieve an item from inventory, pack it and ship it to your customer. Time is money, so the longer each pick takes, the less profit you will get from each order. For e-commerce businesses, pick time is also directly linked to customer satisfaction, so can have a serious impact on your business. Picking, packing and shipping typically involves multiple processes, different staff roles and a variety of equipment, so monitoring the time taken, for each process and your cost per item is a very revealing metric to measure.
Monitor your pick time at regular intervals and ask the following questions:
- Could you invest in automated handling equipment to reduce pick time (e.g. conveyor belts, sorting systems)?
- Does your warehouse layout allow optimum pick times for high demand items?
- Could your picking processes be streamlined or automated?
3) Stock Cover
A stock item costs you money for every day it remains in your warehouse. To keep your overheads to a minimum, warehouses aim to avoid excess stock and make stock turns as short as possible. Measuring the number of days each stock item remains in your warehouse is therefore an important metric. If items are sitting on your shelves for too long, it could be a sign your warehouse is overstocked. This will impact on the time required to locate, pick and ship your items.
4) Accuracy Level
Your order accuracy level reveals how well your operation is running. While aiming for the highest possible accuracy, you should also benchmark your results against averages for your industry. If your competitors are doing better than you at reducing errors, you should consider ways as to improve yours.
A low accuracy level could indicate:
- Room for improvement in your warehouse processes,
- A requirement for more staff training,
- An opportunity for automation,
- Use of barcodes or RFID should be considered if not currently used,
- A need for a new Warehouse Management System (WMS),
- A need for more warehouse staff.
Free Logistics Management Resources From LPC
Our new, free e-book; Continuous Improvement: How To Fine Tune, Improve & Evolve Your Warehouse & Logistics Performance, is full of helpful information about using KPI’s to boost your productivity. Click here to access your copy. To speak with one of our consultants about the KPIs you should be monitoring, call us on 01285 640 038.
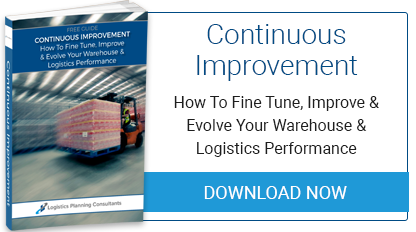