Transport Planning & Optimisation: A Guide From LPC International Ltd, UK Transport Planning Consultants
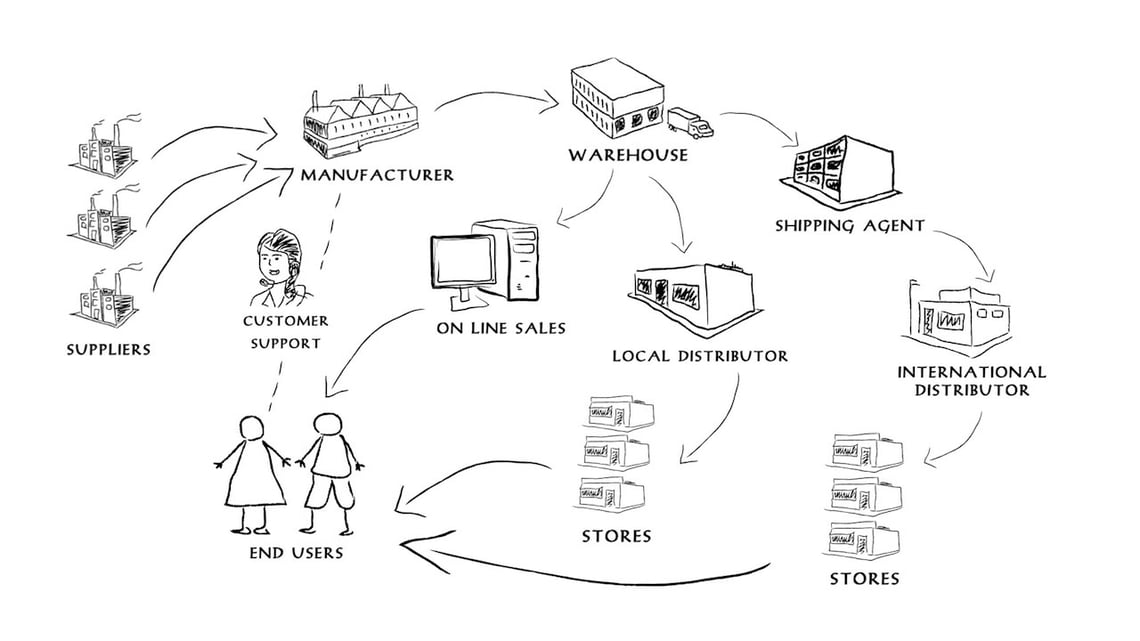
Introduction |
Service Levels |
Fleet Sizes and Profiles |
Other Considerations |
Network Design |
Outsourcing |
Putting It All Together |
Transport & Logistics Planning
Introduction To Transport Planning
Transport planning, optimisation and execution are about minimising costs to meet a required level of service. Keeping costs low and customer satisfaction high is a trade-off, with the latter usually having priority and thus limiting the former.
This free guide will cover the areas that need to be looked at to minimise transport costs and is designed for companies that need to expand, review or optimise their transport and distribution networks. Every company has different needs and requirements to get their products to the customer, and many operate in dynamic and changing environments. Transport is also but one link in a company’s supply chain. A guide on transport planning and transport logistics, therefore, has a very wide field to cover. To help navigate you through this field, we have split this guide into five sections.
- Levels of Service
- Fleet sizes and profiles
- Other Considerations
- Network Design
- Outsourcing.
This guide is not about how you determine your supply chain strategy (which we will cover in a future ebook) and we have therefore made some assumptions around your main facilities remaining in their current locations
Service Levels
Every operation delivering to customers has service levels whether explicitly stated to the customer or not. Tighter or higher service levels have the potential to drive up costs and drive down efficiency. You need to consider and understand the cost to serve. Transport is a service provider within your business and as a consequence has to deliver service levels agreed with the customer by your Sales Department. It can be easy for Sales to promise higher and higher service levels to customers if the cost of delivery does not come out of their budget. However, Logistics and Distribution carries much of the cost to serve, so it is in that department’s interest to check the truly required service levels.
Service levels are usually agreed to and set by the Sales Department and fulfilled by the Transport operation. Whether the level of service committed to is actually demanded and expected is another matter. Few businesses have Amazon’s drop density to allow them to minimize the cost per drop even with near-universal next day delivery and a growing same-day offering.
To minimise the cost per delivery and maximise transport utilisation and efficiency, a constant effort to maximised drop density must be maintained. The following is a list of things to consider in this pursuit:
- Minimising delivery frequency and maximising order size – What is driving a customer’s delivery frequency? Short shelf life? Lack of storage space? Lack of organisation regarding orders? Because it was offered by your company or has always been this way?. It is important to periodically revise and justify delivery frequencies and service levels.
- Postcode to weekday matrix – Maximising drop density leads to maximising fleet utilisation and minimising cost per delivery. We have found that a well designed and maintained postcode to weekday matrix can be almost as efficient as having an open five-day window to deliver in.
- Nominated days – There is a growing trend towards offering free or subsidised delivery. This is bad enough for the bottom line and can be crippling if the delivery frequency is not controlled. One way to control frequency whilst not alienating the customer is to offer free or discounted delivery on a nominated day but charge any other delivery day at cost. This is a test of the truly required delivery frequency.
- Prevention of service level creep – This can manifest itself in the form of increasing delivery frequencies or changes in nominated delivery days or windows which can disrupt well-developed routes.
Figures 1 and 2 below illustrate part of a study where frequencies were reduced to two deliveries a week and deliveries subject to the postcode to weekday allocation shown. The region with the least benefit (not shown) had a potential of a 15% saving and the best had an opportunity of a 27% saving. The company’s overall benefit was 22%. The postcode to weekday matrices also removed any peak days with the same number of vehicles required daily across the week by every depot.
Figure #1 Figure #2
The impact of varying service levels can be modelled and cost in order to justify them. Among the areas that can be investigated is the cost of:
- increasing delivery frequency,
- narrowing delivery windows,
- increasing the use of booked times,
- introducing shorter lead times and
- not penalising avoidable emergency or afterthought orders.
Delivery times, schedules and formats once agreed can be difficult to change but should be reviewed on a regular basis to consider the potential for improvement.
Fleet Sizes and Profiles
Vehicle & Resource Utilisation
Fleet utilisation both in terms of fill and hours is an assessment of efficiency and productivity. Whatever vehicles are used the information on usage is available from your driver tracking system so can be collated and measured. Similarly, you should know how many pallets/cages/cartons/parcels comprise each delivery and therefore can calculate vehicle fill. Calculating the utilisation won’t tell you if you have the most efficient solution but it will tell you how efficiently you are using your solution.
- Can your fleet be better utilised?
- Is a dedicated transport operation optimal? Or would it be more economical to use subcontractors, parcels or pallet carriers?
- Are your vehicle fleet size, type, and geographic spread still optimal?
Planning
Having worked out your utilisation and identified where the underutilised vehicles are and spare capacity exists, you can review your route planning. Whether you do it manually or use one of the planning software solutions available you are looking to minimise fleet size, distance driven and drivers’ hours. You might be able to eliminate routes and reduce your resources through better planning, but some opportunities require analysis and testing, which can be accomplished by running scenarios using modelling or route planning software.
Key Drivers
Each distribution location within a network will have different customer and demand profiles requiring different fleet sizes and profile requirements. Additionally, these profiles may shift with service levels. Influencing factors include:
- Order Frequency and Size - If orders per customer are getting more frequent but overall sales are not growing, then it follows that smaller vehicles will be required. Conversely, if sales increase but orders remain static or fall, then larger vehicles will eventually be required.
- Network Size – If there are only one or two locations in the network covering large territories, then vehicles serving the edges of these territories will spend most of their shift covering stem mileage and with less shift time for delivery worktime; therefore they will need to be smaller. Conversely, as the number of delivery locations in a network increases, average delivery proximity and drop density will increase as well. This means that vehicles need to spend less time driving and have more time for deliveries, thus increasing the need for size.
- Drop Density – Urban areas will have higher drop density so may make use of bigger vehicles up to the point of restrictions and accessibility.
- Congestion – Rigid vehicles are the only practical solution in some urban areas.
- Access and Restrictions – some customers may have access limitations restricting the size of vehicles that can serve them.
- Equipment – Some customers may be able to side offload, others may have docks for rear offloading and others may require tail lifts.
Ultimately the fleet size and profile must be such that vehicles high fill with minimum trips. In other words for example:
- If a vehicle is consistently 50% full then it ought to be downsized
- If a vehicle is consistently having to make second or third trips, then it must be upsized, unless there are access issues limiting vehicle size.
Support From Carriers
It is likely that the fringes of a delivery area are cheaper for a pallet or parcel carrier to serve than on an in-house vehicle because carriers will have other business in the area and a more extensive delivery network like those seen in Figures 3 and 4 on page 12.
It is possible with modelling to determine the economic number and profile of the in-house fleet, what orders it should carry and what orders are more economic to send by the carrier. What needs to be noted is that each additional in-house vehicle has a lower margin of saving relative to its loads going by the carrier, up to the point when the Nth in-house vehicle offers no saving and subsequent additions to the fleet add cost up to the point of N+X where all the work is done by the in-house fleet with no carrier support.
Summary
Ultimately the fleet needs to be reviewed periodically to confirm that:
- Deliveries are optimally allocated between sites
- The fleet size and profile is right at each site
- Maximum fleet utilisation is being achieved at each site
- Maximising average fill by weight and/or volume
- Minimum multi-tripping
- The optimum in-house fleet to carrier ratio is being sustained
Other Considerations
Vehicle Choices
There is a very wide choice of vehicles available, both in size and configuration and equipment. It is also important to consider how you operate them. While operating cost and fuel efficiency are very important, inappropriately sized or equipped vehicles will lead to higher running costs. Note that you may not be able to properly identify what your correct requirements are until you have had your distribution network properly modelled. Your choice of vehicle can have implications for your operation:
- Are your vehicle's side or end loaded?
- Do they interface with your warehouse correctly?
- How are they off-loaded at their destination?
- Do you use tail lifts or carry MHE (mechanical handling equipment)?
- Who loads and unloads at the vehicles’ depot? It is better if the warehouse does this so that more the drivers’ shift time is available for deliveries.
- Are multi-day routes common making sleeper cab vehicles cheaper than regular hotel bills?
The integration of your vehicles into your operation needs to be considered. For example, at your premises side loading and unloading can be quicker than tail loading and unloading. This will affect your turn round times and impact on the number of trips that can be made and therefore the number of vehicles that you need.
At your delivery destinations, do you have tails lifts for locations where manual unloading at ground level is required? If not unloading will be slower and potentially involving poor operating procedures. The result is a reduction in the number of drops that can be made, requiring more vehicles in the operation than otherwise necessary. There may be regulatory issues resulting from poor procedures for which you have liability in the event of an incident.
Periodically a business will renew its vehicle fleet. However, businesses change over time and with that their fleet size and composition requirements. If this is not taken into account and the implications are not considered, the vehicle fleet may be replaced with more of the same instead of something more appropriate.
The operation should be reviewed prior to a fleet renewal to determine if the requirement is still the same and if not, what the new requirement is. The areas to investigate are:
- Do you operate a basic routing plan based on the use of backbone or skeleton routes?
- If so, are those skeleton routes still valid or can they be improved moving forwards?
- Are your customer master file restrictions or service requirements still valid?
- Is a customer marked as restricted to a maximum vehicle size of X because it really is or because it is habitually served by a vehicle of size X?
- Have Sales changed agreed delivery days and times without consulting Transport?
- Is there a real reason behind narrow delivery windows or booked times?
Returns
Returns can consist of customer returns, or equipment, such as pallets, cages and totes, and waste such as cardboard and plastics being bought back for processing. How these are loaded and managed can affect the efficiency of the transport operation and the potential for return loads and inbound logistics to reduce costs or earn revenue.
Inbound Logistics
Whether operating an in house or outsourced transport operation, it is worth determining the potential savings of moving your suppliers to factory gate pricing rather than accepting a delivered price. Collecting your inbound goods on the return leg of an outbound journey will reduce empty running miles as well as saving money on the cost of your purchases.
This analysis of opportunity ties in with the following:
- Warehouse operations in that inbound arrivals must be within the correct window as set by the warehouse.
- Service levels in that some customer’s strict booking times may render backhaul opportunities unviable.
- Transport planning to marry the best fit between a secondary delivery trip and a primary inbound collection.
- Other third-party opportunities where un-associated loads may be available for carriage. These may only be opportunistic and not able to be included in upfront modelling.
Integration With Warehouse Operations
Warehouse and transport operations need to be in tune to minimise any adverse impact on each other and minimise the overall cost. The least expensive transport solution may well lead to increased costs in the warehouse.
Where existing facilities are retained in the model actual costs can be used, otherwise agreed estimated fixed and calculated variable costs are used in the modelling. The facility requirements resulting from the transport solution i.e. the numbers and types of doors/docks, vehicle staging areas, reticulation and gatehouse lanes and queues should be taken into account. In addition, the storage and operational requirements are conceptualised in order to enable correct sizing and costing of the facility both for fixed and variable costs.
Transport Planning
There is an array of routing and scheduling packages in the market and suppliers that focus on the size of the company or market sectors. With the right product for your business, you can:
- Minimize fleet size
- Cut fuel and CO2 emissions
- Improve customer service
- Reduce planning time
- Be more efficient in minimising resource requirements and cost.
- Link with tracking
- Review KPIs
Network Design
Whilst we do illustrate some “blue sky” concepts, true blue-sky opportunities are rare and most network developments start with some legacy locations which influence the final network. All distribution operations will require periodic reviews. The drivers may be:
- New customers,
- Changes in order profiles,
- Changes in delivery requirements,
- Consolidation opportunities due to business acquisition,
- Reduced lead times,
- Continued pressures to reduce costs,
- Outgrowing existing infrastructure,
- Existing infrastructure is no longer optimal with distribution centres in the wrong place.
The design of a distribution network depends on the nature of the business and any legacy constraints it may have. If the company in question is a nationwide parcel carrier then it would want a network that maximises the number of deliveries per vehicle shift such as that in Figure 4 where most drops can be reached within an hour thus minimising stem driving time. If the company’s delivery profile comprises fewer drops per route and is driven more by volume and unloading time then something like Figures 4 and 5 may be more suitable depending on the legacy infrastructure and customer base. A network like Figure 3 will allow enabling the reaching of most customers within two hours and a network like Figure 5 within the companies delivering mainly full loads will want as few distribution locations as required to avoid overnight stops. Overnight stops reduce the vehicle’s utilisation because it cannot be double shifted and because, unless there is a backhaul opportunity or a second trip on day 2, the average vehicle fill per day is limited to a maximum of 50% (one load over two days). Often the distribution sites for full load are factories or shipping ports themselves because often, and up to a point, the cheapest network option is the one with minimum trunking and double handling requirements.
Figure #3 Figure #4 Figure #5
The above maps only consider transport costs. In reality, warehousing and stockholding costs are at least as important and therefore the overall cheapest network will have fewer locations than the cheapest transport network. Typically, as the number of warehouses increases so do property, stock, storage and handling costs, but transport costs decrease (assuming the warehouses are properly located and boundaries between them properly defined). Therefore for every business, there is an NDC/RDC/Out-base profile sweet spot which presents the lowest distribution cost for a given service level. For a smaller company, this might be a single warehouse. Computer modelling can be used to find the optimum logistics network for your company. The economic impact of opening or closing one or more locations can also be modelled if you are considering expanding or rationalising your warehouse locations
Figure #6
A full review may be more than you wish to undertake, but some of the potential options such as the use of out-bases can extend the “reach” of your transport operation. For example, one of the potential scenarios could be the use of out-bases, be they stockless or semi stocked, carrying only a few faster-moving SKUs to ensure service levels. If stockless these would function as drop off points for trailers or drop bodies that can increase the achievable delivery distance for loads or act as a node for deliveries that could not be done from an existing facility and thus increasing the number of drops that can be carried out in a given period.
Network Design As An Enabler
Network design is normally viewed as a way of reducing cost, but sometimes network design is necessary to enable a business to grow or to offer services not possible with the existing setup.
A case in point is illustrated by Figure 7 where the business in question was servicing all its customers from its only location. The consequence of this set-up was:
- Early morning deliveries could not be made in time. This was particularly important in the Southeast, its biggest customer base, so early delivery orders had to be sent by specialist carriers at relatively great expense.
- There was new business available that could not be gained because of this constraint.
- It was hard to collect from suppliers on the return leg because of timings and shift lengths.
The solution in Figure 8 was more expensive in the short term because it included the cost of cross-docking yards and trunking, but beneficial overall because:
- Early morning deliveries could be brought onto the in-house fleet thus recovering the carrier expenses.
- The available new business could now be pursued and growth could restart.
- Backhaul from suppliers was more streamlined.
- Overall, the bottom line was expected to grow.
Figure #7 Figure #8
Outsourcing
In the previous sections, we have looked at getting a better understanding of your current operation and how to improve it. In this section, we look at outsourcing to a third party. The third-party will not have the same constraints as your operation and be in a position to offer different choices to deliver to your customers.
First, you must never outsource your distribution because it has got a problem. The fundamental processes must all work well enough before outsourcing. Unless the problem is a lack of specific expertise that is offered by the third party, it is unlikely to go away when it is outsourced. Rather, it will just be dealt with in the existing way by a third party that will charge you for the privilege. Additionally, it may prove more difficult and expensive to make changes to the operation once it is outsourced.
The options (choices) available to you revolve around:
- Part or wholly outsourced.
- Dedicated or single user.
- Multi-user or shared user.
The decision on whether to keep transport in-house or to outsource it is normally influenced by whether:
- It is deemed to be a core competence of your business
- It is a key part of your service promise or key to your customer experience.
- There is a place or desire for managing transport within your business.
- There is a need for change one way or the other
- There is a need for logistics expertise or innovation
- Transport is perceived as being too expensive
As with any decision, there are advantages and disadvantages to a third party, some of which are:
Advantages of Outsourcing
- Expertise: the management of a transport operation and fleet is the contractor’s forte
- Utilisation; a 3rd party making better use of their fleet will be more economic
- Better service: with a widely spread customer base, using a shared fleet can offer more options to deliver to different areas.
- Greater coverage; with a 3rd party pallet or parcel carrier delivering longer distances leaving local deliveries with the in-house fleet.
- There is also the potential to use a 3rd party for both warehousing and transport if their facilities are more appropriately located for your customer base.
Disadvantages of Outsourcing
- Cost - there is the potential for it to be more expensive
- Control - a degree of control is lost especially if the contract is not properly tied down with achievable service levels and penalties.
- Change - this can have contractual considerations and take longer to achieve.
Potential Solutions
Wholly in-house or outsourced is fairly self-explanatory, but there is the opportunity for a hybrid solution. This is where some elements of distribution are kept in house, while others are outsourced. The potential solutions depend on many factors including:
- Company size, number of facilities,
- Number of customers and their locations,
- Business sector.
For example, a company with multiple DCs may outsource the transport from some and have in-house transport in others, or for a single warehouse, the delivery operation might be in-house for near or large customers and be outsourced for customers further away or who are small in size.
Outsourced Options
The type of service contracted will very much depend on:
- The size of the requirement,
- The nature of the product delivered,
- The types of and the service levels required and,
- Cost.
Typically, in decreasing order of service level and cost, the list would look like this:
- 3PL (or in house) for a dedicated solution
- Shared user for sharing resources with a suitable co-user(s) that has similar service level requirements to that of your business.
- Multiuser where lower costs are important.
- Pallet networks or couriers
Validation of Options
Depending on the reasons for outsourcing, some validation of your objectives may be appropriate before embarking on the outsourcing process. This can involve considerable management time and expense. For example, if cost is one of them, then what are realistic savings expectations given the uniformity of the cost base within the logistics industry and the low margin nature of the 3PL transport element?
Another reason for possible outsourcing is to be in the correct place in order to meet your customers’ orders in the most cost-effective way. Being in the correct place may allow you to save money on outbound deliveries, which could be used to improve your margins or reduce your prices, be more competitive leading to more sales. For an SME a simple Centre of Gravity study will indicate where your central and distribution centre should ideally be based. If you have a larger operation and need multiple DCs, there will be a more complex and iterative process of modelling and several C of G type studies will be required.
If the ideal location(s) for your operation is (are) well away from your existing facilities this might also prompt you to consider outsourcing the warehouse operation in addition to the transport to a 3PL in the area you need to be in, as a simpler means of moving the operation.
The Process of Outsourcing
The actual process of choosing a suitable company to partner with and outsourcing the operation can be a major undertaking. It can be broken down into a number of steps as follows:
- Create project team and resource
- Identifying potentially suitable contractors
- Creating a tender package
- Issuing, managing the tender process
- Assess responses
- Contract negotiations and awarding the contract
- Implementation
The Project Team
The process can take a lot of time and requires expertise and resource. A project team should be established. Many members of the team will contribute only part-time as they have their “day jobs” to do in operations or IT etc. If particular expertise is required consideration should be given to using external support.
Identifying Appropriate Contractors
The purpose of a tender is to obtain accurate competitive quotations from serious service providers who are capable of delivering the service your business requires. Three such quotations would be the absolute minimum you need, but five or six would be better allowing you to shortlist a preferred two or three for final discussions.
You might know suitable suppliers from experience or knowledge of your industry, otherwise, look at members of an appropriate trade body or seek outside advice. After you have identified potential suppliers, you should then establish that they are interested and have the capability to both respond to your tender and fulfil the contract prior to issuing the actual tender documents.
This could be done by issuing a pre-tender Request for Information (RFI) to establish who is willing and able. The RFI should contain:
- Overview of your company and operation to be outsourced
- Objectives for outsourcing, - better service, cost reduction, etc.
- Summary information/data outlining size and scope of the operation
- Project timeframe
- Summary of information required from a potential bidder
The information required should naturally include details about the contractor and their capabilities, and confirmation of their willingness to tender and capability to undertake it. You should also request case studies and information about similar operations to yours that they support. If the information and data you supplied are detailed enough, indicative budget costs could be requested. The budget costs will give a comparison against current in-house costs and help validate the business case and steer the strategy.
Collate and assess the information supplied from the contractors and identify your tender list. At this point you are not selecting the contractor you will award a contract to, but those contractors who would be capable of doing the job if they put in a competitive tender in the next stage. Your RFI approach is narrowing the field and reducing timewasting at the next stage.
The Tender Creation - The tender process is not only about you selecting the best contractor it is also about making the contractor want to work with you. Contractors can spend a lot of money and use a lot of resources responding to tenders. You want them to be very interested in you and to put their “A-Team” onto their response. It is not something you can ensure but clear concise, complete tender documents supported by data with stated assumptions to be used where data is unavailable goes a long way. It shows you are serious, have thought the process through, and have done your best to assist them in responding without them wasting time asking for clarification, further information, or having to make their own assumptions.
The objective of the tender is to create a level playing field for all respondents with no room for “favourable assumptions” to be made by a contractor to support their bid or for wrong assumptions that potentially mean the expectation from the best response is not realised. One of the ways to ensure that the contractor has not made assumptions is to request a base case transport model from them to prove that their outputs are realistic. Responding to tenders is an analytical process and the accuracy of the proposed solutions and responses will be directly influenced by the quality of the data and document issued. You should bear in mind that one of the main reasons for the failure of 3PL contracts is because the solutions developed were done so on incomplete or incorrect operational data. We cover some of the data and information you should include below.
Data
The accuracy of a transport tender response in terms of the calculated resource requirement and its cost is directly proportional to the quality of the delivery data, parameters and statements included in the tender. The information pack should include not only historical delivery and collect data but also all the applicable restrictions, parameters and prescriptions to ensure:
- A level playing field by limiting divergence between respondents due to assumptions made.
- Errors are consistent amongst all respondents given that there will always be a level of inaccuracy in any resource requirement calculation.
Below is a guide of data requirements for transport and distribution modelling.
Customer master data including:
- Customer code
- Address and especially postcode for grid referencing of digitised road map
- Time windows
- Vehicle restrictions.
- Special unloading time requirements if different to the default used if applicable.
Delivery or collection records including:
- Customer code to link the record to customer address
- Delivery date
- Booked time if applicable
- The volume delivered (collected) by unit load (pallets, cages, cubes, kilos, cases, as required)
Parameters
- Vehicle capacities by vehicle type and per unit load – particularly for unconventional vehicle sizes or unit loads.
- Typical fixed and variable loading times at delivery.
- Typical fixed and variable loading times at depot (if client’s depots are to be used)
Assumptions
Sometimes operational data is incomplete or not known. When this is the case it pays to invest time to either research such things (like booked times or unloading rates) or you must state the parameters and assumptions for all respondents to use, including the incumbent service provider. Faced with a lack of prescriptive detail respondents will make and state assumptions which lead to at least two problems:
- Assumptions and therefore parameters used will differ between respondents
- Respondents may make unrealistic assumptions leading to some responses appearing artificially economic or expensive relative to that of the incumbent party.
Descriptive & Other Information
It is important to describe the distribution operation being put out to tender. Data alone can lead to the design and costing of an accurate solution for a misunderstood operation. The information to include would be all the things that are not part of data and parameters including but not limited to:
- Loading and reloading issues
- Drivers’ pre-shift allowance – do they have to contribute to the loading of their vehicle?
- Earliest loading times or departure times
- Are vehicles loaded overnight and ready to depart whenever?
- Is the site(s) under urban restrictions limiting the earliest vehicle departures?
- Are there site capacities limiting the number of vehicles that can be loaded or reloaded at any given time?
- Unloading issues
- Latest return times
- Drivers’ duties and time budget upon return
- Trunking requirements and timings
- To establish whether and how much of the fleet can be double shifted for trunking
- How things work
- Trunking requirements and timings
- To establish whether and how much of the fleet can be double shifted for trunking
- How things work
- A day in the life of (DILO).
Summary
Data collection beyond historical delivery, or collection, records may be challenging for some companies. However, it is important that a reasonable effort is made to source sufficient correct data to enable accurate resource calculations and real like with like comparisons between bidders.
What must be avoided is a situation where a contract is awarded to a response drawn up without the required level of detail. This will only lead to the wrong decision which in turn will lead to escalating costs and a breakdown in the relationship between client and contractor. If the data and information supplied was accurate and complete, then the solutions presented by the bidders would each be accurate and representative of the bidders’ capacities, for there would have been little room for assumptions. It follows that all responses are comparing like with like and with that of the incumbent contractor.
However, if the data and information are incorrect or have gaps in them, then these gaps will be plugged in with assumptions, and probably of the kind favourable to the bidder. Examples of gaps include:
- Stating in the text that many or all deliveries have booked times but not providing these in the data.
- Omitting loading and unloading times and leaving respondents to use their own assumptions.
- Not providing a prescription for anything else that can be interpreted in different ways by different respondents.
Yes, all assumptions will be stated, but by then it is too late for it will not be possible to determine the margins of error within the solutions proposed, and therefore it will not be possible to compare responses on a like with like basis.
Other Information
The tender pack should also include:
- Non-disclosure agreement
- Any particular scenario or defined solution that the contractors should bid against
- Tender response process and timeframe
- Contract programme
- IT requirements/connectivity to business systems
- TUPE
- Terms and conditions.
Issuing the Tender and Managing the Process
In general, the better the tender pack the less complicated and time consuming the tender process will be for everyone. Sufficient time should be allowed for the contractors to formulate their solutions and respond to the tender. The length of time will depend on the size and complexity of the operation to be tendered but would usually be between 3 and 6 weeks.
However good the tender package is there will be some questions. To be fair to the bidders there should be a process to share with all respondents answers to questions asked by all respondents
Many companies and organisations have rules and procedures in their corporate governance for issuing and receiving tender and their responses. These will need to be taken into account.
Assess Responses
The responses are received, hopefully from all the contractors, you issued the tender. You now need to review and understand the responses. It is likely that there will be differences between the responses and maybe some questions to clarify what has been submitted.
You should consider the criteria you will use to assess the responses. There are several potential criteria that you could include:
- Price and cost,
- Service levels,
- Compatibility of culture,
- IT systems and integration,
- Location,
- Quality of response,
- Experience with similar contracts.
An assessment system could be devised to score the responses against each of the criteria. The criteria scores would then be weighted as not all criteria have the same importance. For example, price is much more important than the quality of response documents. This allows for a more balanced approach than simply who is the cheapest without assessing the value of what is offered.
Contract Negotiations & Awarding The Contract
From the assessment process, you will have a preferred bidder to open negotiations with. You should also have a second preference as you may not be able to conclude a satisfactory contract with your first preference.
There are standard contract forms, or you can use your own. Using and modifying a standard form if necessary is generally quicker than a bespoke contract, as it is likely that your preferred contractor is familiar with it. You will need a lawyer to review the legal aspects, but you will need to ensure that the details of the service to be provided and remuneration are correct and that the remedies for any shortfall in performance are suitable and applicable. These details are usually in the schedules of the contract. The lawyers can help enforce what is in the schedules, but they may not be familiar with the logistical and operational details of what you are outsourcing. If you do not have the expertise in-house it might be prudent to retain external support.
Implementation
Given the potential range of services and the different sizes of contracts that different companies can outsource it is difficult to offer specific advice on implementation. However, there are two things that are always required – a plan and resources.
The plan should cover the implementation from the award of the contract up to and beyond the go-live date so that the initial run-up period is covered. The work to be done in the implementation should be identified and then be broken down into a series of tasks that need to be accomplished with a due date and who will deliver the task identified.
Many of the tasks will be down to the contractor to deliver, but equally many will be down to you or your team. This is where the resource comes in. Sufficient people of the right skills and seniority need to be allocated to the implementation with the time to fulfil the tasks identified. Bear in mind that if you expect people with demanding roles in your company to be part of the process, the dynamics of their “day job” often impact their time and role in an implementation team.
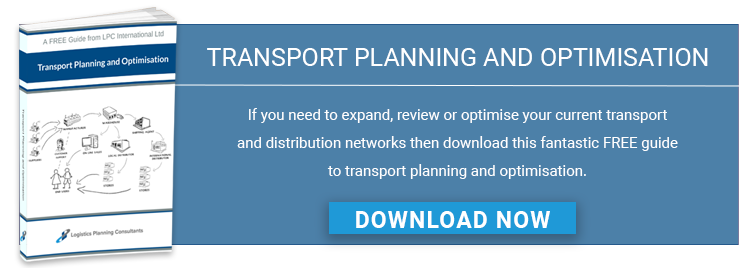
Putting It All Together
Very few operations are unchanged over time, and an optimal solution from yesterday might not be the optimal solution for tomorrow. If you establish your metrics and KPIs and constantly review them, you can measure your efficiency and productivity and costs. Where you see the change you can investigate and then look at your options.
A significant change in your business is also a signal and an opportunity to review your operation and consider your options, both in-house and outsourced.
Transport planning and optimisation is an ongoing process with periodic reviews which may identify a range of required changes to the fleet and/or network. In this e-book, we have covered the areas that need to be reviewed. In short:
- Are you overdelivering on service levels?
- Are you using your fleet optimally?
- Do you have the right fleet mix?
- Is the right fleet in the right place?
- Does your network have any weaknesses?
- What outsourcing alternatives are suitable for your business?
The drive to optimise your operation can lead to a review of your whole network and the supply chain strategy behind it. This is easier said than done and often is only possible with the use of sophisticated modelling tools. We have the tools and the expertise to assist your company in its quest to optimise its transport solution.
- First, we begin with reviewing, understanding and optimising your current transport operation.
- We then consider how you change and improve your operation taking into account such factors as the impact of customer service promises, operational issues and fleet size, profile and vehicle design.
- Next, we consider whether the network needs to be improved
- Finally, we look at the different transport and operational choices available, to what degree outsourcing may offer benefits and how you go about it.
Analysis & Scenarios
The use of modelling software allows any distribution operation to be set up in a virtual model using actual operational data so that potential solutions – known as scenarios – can be modelled and evaluated. There are various modelling packages available. Some have a more black-box approach than others, but they generally allow you to model the routes from your facilities, to vary and modify the number and location of those facilities and to model options using any combination of some or all of national, regional or local
distribution centres and stockless outbases, drop off points or transport yards. Our preferred approach to modelling starts with the building of a transparent base case model of your business with as much accuracy and detail as your data allows. This model is then compared to reality to ensure that it is representative and a sound base from which to develop scenarios in a like for like way. Therefore the process is started as a review of the current operation taking into account all areas that will need to be analysed and modelled. This gives an “As Is” model, or a baseline against which further scenarios can be compared. It also serves to ensure that the model is correct and that the results it gives properly mimic the actual transport KPIs and costs that are in use. The model can initially be run using your current locations and facilities, but we can take it further and look at future possible networks.
Typically, as the number of warehouses increases so do property, stock, storage and handling costs. However, transport costs decrease assuming the warehouses are properly located and boundaries between them properly defined. Therefore, for every business, there is an NDC / RDC / Out-base profile sweet spot which presents the lowest distribution cost for a given service level. For a smaller company, this might be a single warehouse.
Computer modelling can be used to find the optimum logistics network for your company. It can also accurately model the economic impact of various possibilities such as:
- Opening or closing one or more distribution locations if you are considering expanding or rationalising your warehouse locations.
- Growth in business
- Loss of business
- Changes in service levels.
- Greater or lesser use of carriers.
Conclusion
We trust that this e-book will help you in your quest to improve your transport and distribution operation by drawing your attention to the breadth of issues that need to be considered. However, all change is challenging and more so without the right tools and expertise.
We have the tools and expertise to support you and look forward to the opportunity to assist you and your team on your journey of improvement.
Talk To One Of Our Transport Planning Consultants
Book a FREE Transport & Logistics Healthcheck and get some free consulting from one of our UK Transport Planning Consultants.