Project Overview
DSG International Mixed Electricals comprising Curry’s and Dixons, undertook an end-to-end supply chain review. The findings of this review identified the opportunity to fully re-organise its distribution network into an efficient centralised and cost effective operating model.
The network included local distribution centers which stocked faster moving lines which supported branch and home delivery sales; supplemented by stock from two Regional Distribution Centers (RDC’s). There were a further two separate facilities – an NDC providing a branch delivery service of small fast moving lines, and a customer fulfillment Centre for e-commerce orders.
The proposed strategy centres on the supply chain to the Newark Campus and an RDC in Bristol.
With DSG; Branch Deliveries were being served from the RDC which had 467,000 square foot of available floor space and a Small Products Warehouse (SPW) with 233,000 square foot of space, which was supported by the Bristol RDC which had 250,000 square foot of floor space.
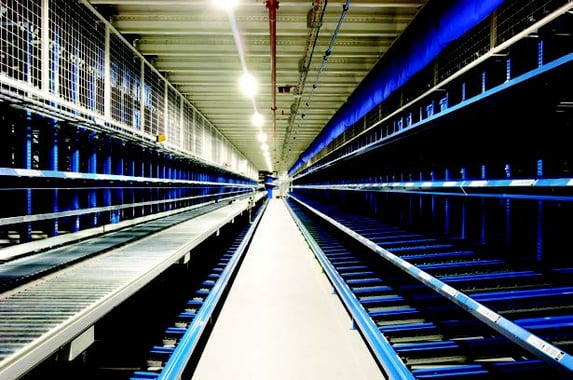
The Newark Campus was home to the Central Home Delivery Centre (CHDC) of 690,000 square foot and a central returns point of 180,000 square foot.
The LDCs have been replaced with a network of stockless cross dock centres to give home delivery coverage and outbases for the branch deliveries to achieve full coverage. The size of the SPW was determined as part of the initial review. However, DSGI recognised that the design of the material handling systems and the interior layout of the SPW required specialised skills not available within Group and external consultancy support was required for which LPC were retained.
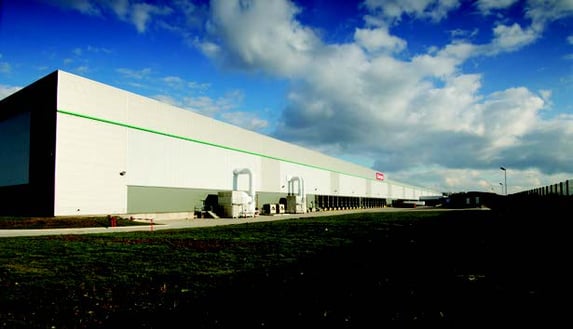
The scope of support required was split into three phases. (Click to jump to a section)
• To understand the business requirements, overall scope of supply chain re-development and the links between SPW and RDC.
• Analysis for peak and average period of the order, purchasing, stockholding data and quantification of the material flows and process requirements.
• Sizing taking into account growth projections and allowances taking into account the building which was already designed by other third parties.
• Preparation of a Data Analysis Report and Data Pack.
• Defining the space and layout requirements producing a concept specification to form the basis of the tender process. The tender responses needed to be assessed against a single base design and indicated to the potential suppliers the processes and levels of automation that would be acceptable in terms of complexity, capital expenditure and revenue costs.
• Production of a detailed tender documentation including equipment specifications, building interface specification, CAD drawings and data pack.
• Production of a ‘Suitability of Options’ summary report.
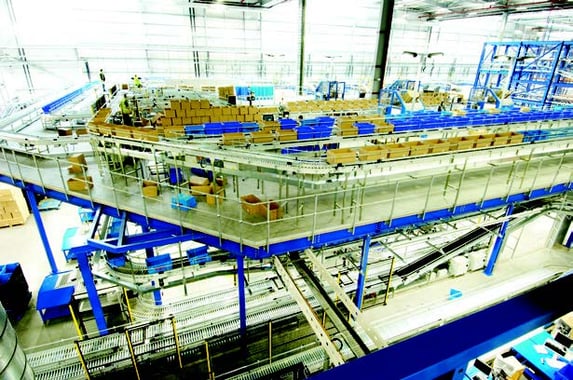
Phase 1 Solution Concept:
LPC provided a solution to deliver the capability required to support the branch network with small products delivered in totes and cartons, and internet customers with the full range of group products except those requiring two man delivery.
The solution was proposed in order to:-
• Support growth for material handling.
• Provide 5,000 pick from tote locations in two tote silos.
• 1,000 pick from pallet locations in two pallet live silos.
• Automatically handle and store totes for storage and picking.
• Control manually operated Very Narrow Aisle racking, reach and order picking trucks for movement and handling of pallets.
• Erect or induct cartons and totes and convey between picking, packing and despatch to satisfy orders.
Equipment Supplier
Vendor Selection
• Listing of potential vendors meeting mechanical handling requirements provided.
• An RFI (Request for Information) was produced and sent to selected suppliers. Reference sites were also requested at this stage.
• Creation of Preferred Vendor Shortlist.
Tender Process
• An RFP (Request for Proposal) containing specifications, drawings and data was sent.
• Management of the tender process involving, answering queries, presentations, site tours of existing and new facilities.
• Assessment, evaluation and detailed review of tender responses, presentations and reference visits.
• Advice on suitability of proposed control systems.
• Advice on areas of improvement and enhancement of supplier offers.
Contract Negotiations
• Attendance at contract negotiations providing technical input to support DSGI’s legal team in defining the technical and testing specifications to be met.
• Advice on contracting achievable system performance levels and potential penalties.
Building Interface
• Providing technical input into the building shell specification e.g. concrete floor reinforcement for tote cranes to allow installation to proceed to programme.
In Conclusion
After discussion & debate with DSGi it was agreed that the preferred supplier would be Dematic as the contractor responsible for supplying a turnkey solution of the all mechanical handling and storage equipment together with a warehouse control system.
LPC further assisted;
System Detailed Design
• Final MHE Design & Development in conjunction with Dematic.
• Review of Dematic System Simulation.
• Review of drawings and specifications produced by Dem
• Support to IS and Operations in reviewing the Functional Design Specification produced by Dematic.
• Design and production of specifications for the procurement of storage totes, despatch totes, cartons and consumables.
• Co-ordination of Dematic supply with operational fit out.
Role of MHE Engineer
• Manage the MHE activities of the Small Parts Warehouse.
• Act as agent during the fit-out phase.
• Review all drawings produced by the MHE contractor. Sign off and issue to other parties.
• Review, agree and monitor progress of the fit-out of the MHE contractor and ensure that the schedule is capable of and achieves the time scales.
• Review and assess the Dematic Simulation activities including inputs, outputs and assumptions.
• MHE Advice.
• Provide advice as required to DSGI in connection with the project regarding both Dematic activities and other related areas.
• Agree schedule for co-ordinated activities and monitor progress.
• Monitor and check drawings as issued by all parties.
• Oversee the performance and adherence to contract and program.
• Specify protection, lines and signage, snagging of all MHE integrator installed items, mezzanines, racking, cranes, conveying, tote live, carton erectors etc.
• Verify suitability of functional and throughput testing programme as provided by Integrator.
• Carry out functional and throughput testing with Integrator and client representatives.
• Sign takeover certificates on behalf of client.
• Support during start up and ramp up.
Transition Support
• Calculation of manning requirements.
• Advice on sequencing to support transition of three warehouses into SPW.
• Calculation of KPIs (Key Performance Indicators) and budgets.
• Provide early life support during go-live transition.
Operational Support
• Provide support to operational management in the go live period of operation in order to maximise performance.
• Provide input into drawing up SOPs (Standard Operating Procedures) and advice on system parameters.
• Advise on shifts, resource & productivity levels.
• Advise on negotiation, monitoring and performance of the Warehouse Services Agreement whereby Dematic provide maintenance support with guaranteed system availability with penalties for non-performance.
In Conclusion:
The solution was handed over on time and two of the three warehouses were transitioned into the SPW. The third transitioned when the work of integrating the DSGI IT Systems had been complete.